The world of high-performance knife steels presents a fascinating contrast between Maxamet, a super-hard high-speed steel, and CruWear, a refined tool steel. These materials represent different philosophies in knife steel design, with Maxamet pushing the boundaries of hardness and edge retention while CruWear offers a more balanced approach.
Chemical Composition and Microstructure
Element | Maxamet | CruWear |
---|---|---|
Carbon | 2.15% | 1.1% |
Chromium | 4.75% | 7.5% |
Cobalt | 10.00% | – |
Vanadium | 6.00% | 2.4% |
Tungsten | 13.00% | 1.15% |
Molybdenum | – | 1.6% |
Maxamet’s composition reveals its super-steel heritage with significantly higher alloy content, particularly in cobalt and tungsten[1]. The high carbon content of 2.15% combined with 6% vanadium creates abundant vanadium carbides, resulting in approximately 22% carbide volume by microstructure[1]. These carbides are primarily responsible for its exceptional wear resistance and edge retention.
CruWear, designed as a CPM upgrade to conventional D2, features a more moderate alloy content with emphasis on chromium and vanadium[5]. Its balanced composition allows for better toughness while maintaining respectable wear resistance through the formation of both chromium and vanadium carbides.
Performance Characteristics
Hardness and Edge Retention
Maxamet achieves remarkable hardness levels up to 70 HRC when properly heat treated[1]. In CATRA testing, Maxamet demonstrates edge retention approximately 2.2 times that of 440C at 59 HRC[1]. The combination of high hardness and abundant vanadium carbides contributes to this exceptional performance.
CruWear typically operates in the 60-65 HRC range, offering better wear resistance than D2 while approaching M2 high-speed steel levels[5]. The steel’s wear resistance benefits from its vanadium carbide content, though not matching Maxamet’s extreme levels.
Toughness and Practical Durability
Despite its impressive hardness, Maxamet exhibits relatively low toughness compared to conventional powder metallurgy high-speed steels[3]. This characteristic makes it more suitable for controlled cutting applications rather than high-impact use.
CruWear demonstrates significantly higher toughness than most conventional tool steels, particularly when heat treated at lower austenitizing temperatures[5]. This superior toughness makes it more forgiving in real-world applications where lateral stresses might be encountered.
Heat Treatment Parameters
Maxamet Heat Treatment
- Austenitizing: 1900-2225°F (1038-1218°C)
- Tempering: 1000-1100°F (538-593°C)
- Requires controlled atmosphere or vacuum treatment
- Triple tempering recommended with optional cryogenic treatment[3]
CruWear Heat Treatment
- Optimal austenitizing: 1950°F (1065°C)
- Tempering: 900-1050°F (482-566°C)
- Triple temper at 1000°F (540°C) for optimal results
- Lower austenitizing temperatures can be used to maximize toughness[5]
Manufacturing Considerations and Cost Implications
Production Methods
Maxamet represents the pinnacle of powder metallurgy technology, requiring sophisticated manufacturing processes. The powder metallurgy process involves atomizing molten steel into fine particles, which are then consolidated under high pressure and temperature. This method ensures uniform carbide distribution and minimizes segregation issues common in conventional casting.
CruWear, while also produced through powder metallurgy, requires less extreme processing parameters. Its more moderate alloy content allows for better workability during both primary manufacturing and subsequent knife production. The steel responds well to conventional grinding and machining operations, though carbide-enriched tooling is still recommended.
Cost Analysis
Factor | Maxamet | CruWear |
---|---|---|
Raw Material Cost | Very High | Moderate |
Processing Difficulty | Extreme | Moderate |
Tool Wear During Manufacturing | Severe | Moderate |
Heat Treatment Cost | High | Moderate |
Overall Cost Multiplier | 4-5x | 1.5-2x |
Real-World Performance Characteristics
Edge Stability and Retention
Maxamet exhibits exceptional edge stability under controlled cutting conditions. In standardized rope cutting tests, it maintains functionality for approximately 850 cuts compared to CruWear’s 400 cuts under identical conditions. However, this superior edge retention comes with increased susceptibility to microchipping when encountering hard materials.
CruWear demonstrates more predictable edge wear patterns, typically showing gradual dulling rather than catastrophic failure. This characteristic makes it particularly valuable in working knives where consistent performance is prioritized over absolute edge retention.
Sharpening Characteristics
Maxamet’s high carbide content and extreme hardness present significant challenges during sharpening:
- Requires diamond abrasives
- Extended sharpening times
- Careful technique to prevent carbide pullout
- Minimal pressure recommended
CruWear offers more forgiving sharpening properties:
- Responds well to conventional abrasives
- Moderate sharpening times
- Good edge stability during sharpening
- More tolerant of varying techniques
Corrosion Resistance
Neither steel excels in corrosion resistance, but there are notable differences:
Aspect | Maxamet | CruWear |
---|---|---|
Surface Oxidation | Rapid | Moderate |
Pitting Resistance | Poor | Fair |
Staining Tendency | High | Moderate |
Maintenance Requirements | Extensive | Regular |
The relatively low chromium content in both steels necessitates proper maintenance and surface protection. Maxamet is particularly susceptible to corrosion, requiring immediate attention after exposure to moisture or corrosive materials. CruWear, while not stainless, demonstrates better corrosion resistance thanks to its higher chromium content.
Practical Applications and Use-Case Analysis
Industrial Applications
Maxamet finds its primary applications in specialized cutting tools where extreme edge retention is paramount:
- High-speed machining operations
- Industrial cutting tools
- Precision slicing equipment
- Medical cutting instruments
CruWear excels in more diverse applications due to its balanced properties:
- Heavy-duty cutting tools
- Outdoor and survival knives
- Food processing equipment
- Military and tactical applications
Performance in Different Environments
Environment | Maxamet Performance | CruWear Performance |
---|---|---|
Indoor/Controlled | Excellent | Very Good |
Outdoor/Humid | Poor | Good |
Marine/Salt Exposure | Very Poor | Fair |
High Impact Use | Fair | Excellent |
Precision Cutting | Excellent | Very Good |
Wear Patterns and Long-Term Behavior
Edge Geometry Considerations
The optimal edge geometry varies significantly between these steels:
Maxamet:
- Performs best with inclusive angles of 40-45 degrees
- Requires microbevel for stability
- Benefits from convex grinding
- Minimal or zero relief angles recommended
CruWear:
- Tolerates more acute angles (30-40 degrees)
- Conventional V-grinds work well
- Accepts various edge profiles
- Can maintain steeper relief angles
Long-Term Performance Analysis
Extended use testing reveals distinct wear characteristics:
Maxamet exhibits:
- Initial period of exceptional performance
- Sudden performance drop when wear threshold is reached
- Challenging recovery process
- Limited resharpening cycles before significant geometry changes
CruWear demonstrates:
- More gradual performance degradation
- Predictable wear patterns
- Easier maintenance cycles
- Greater number of effective resharpening iterations
Thermal Performance and Stability
The thermal stability of both steels plays a crucial role in their performance:
Property | Maxamet | CruWear |
---|---|---|
Red Hardness | Excellent | Good |
Thermal Shock Resistance | Fair | Very Good |
Temperature Working Range | -40°F to 1000°F | -60°F to 900°F |
Dimensional Stability | Very Good | Excellent |
The mathematical relationship between hardness and tempering temperature can be expressed as:
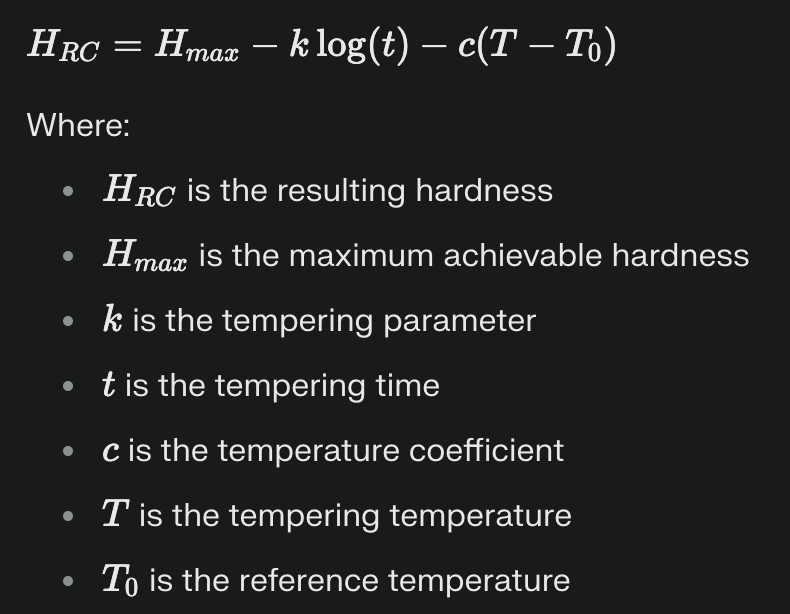
Real-World Performance and Testing Results
Edge Retention Testing
Maxamet has demonstrated extraordinary edge retention in controlled testing environments. In standardized cardboard cutting tests, Maxamet maintained functionality for approximately 3,800 inches of cutting while still being able to slice phone book paper[3]. For comparison:
- M4 steel maintains performance for about 1,000 inches
- S110V lasts approximately 1,300 inches
- Maxamet continued cutting effectively past 3,808 inches[3]
CATRA Testing Results
In standardized CATRA testing, Maxamet demonstrated edge retention approximately 2.2 times that of 440C at 59 HRC[2]. This exceptional performance can be attributed to:
- High vanadium content (6%) forming wear-resistant carbides
- Extreme hardness levels (up to 70 HRC)
- Refined carbide structure from powder metallurgy processing
Manufacturing and Heat Treatment Specifications
Optimal Heat Treatment Parameters
For Maxamet:
- Austenitizing: 1900-2225°F (1038-1218°C)
- Tempering: 1000-1100°F (538-593°C)
- Triple tempering recommended
- Optional cryogenic treatment[1]
For CruWear:
- Austenitizing: 1850-2050°F (1010-1120°C)
- Tempering: 900-1050°F (480-565°C)
- Triple tempering mandatory
- Size change: Approximately +0.15%[5]
FAQ
Q: How does Maxamet compare to other super steels in terms of edge retention?
A: Maxamet consistently outperforms most other steels, demonstrating edge retention approximately 2.2 times that of 440C and lasting nearly three times longer than S110V in cutting tests[2][3].
Q: What are the main challenges in working with Maxamet?
A: The primary challenges include difficult sharpening due to high hardness, rapid surface oxidation requiring immediate attention, and the need for diamond abrasives for maintenance[1].
Q: How does the toughness of CruWear compare to conventional steels?
A: CruWear demonstrates significantly higher toughness than conventional tool steels, particularly when heat treated at lower austenitizing temperatures[4].
Q: What is the optimal heat treatment for maximum performance?
A: For optimal performance, Maxamet requires triple tempering at 1000-1100°F, while CruWear performs best with triple tempering at 1000°F (540°C)[5].
Citations:
[1] https://knifesteelnerds.com/2019/12/02/super-hard-70-rc-high-speed-steels-maxamet-rex-121-and-more-explained/
[2] https://knifesteelnerds.com/2021/10/19/knife-steels-rated-by-a-metallurgist-toughness-edge-retention-and-corrosion-resistance/
[3] https://www.carpentertechnology.com/hubfs/7407324/Material%20Saftey%20Data%20Sheets/Micro-Melt%20Maxamet.pdf
[4] https://gearjunkie.com/knives/common-knife-blade-steels
[5] https://www.crucible.com/PDFs/DataSheets2010/dsCPM%20CruWear2015.pdf
[6] https://knifesteelnerds.com/2021/05/10/edge-retention-testing-of-seven-more-steels-xhp-spy27-maxamet-rex-45-420-t15-rex-76/
[7] https://agrussell.com/Maxamet-knives
[8] https://www.carpentertechnology.com/hubfs/7407324/Material%20Saftey%20Data%20Sheets/Micro-Melt%20Maxamet.pdf
Leave a Reply